New Article on Closed-loop real-time optimization for unsteady operating production
21.04.2022
Andreas Himmel, Rolf Findeisen, Kai Sundmacher
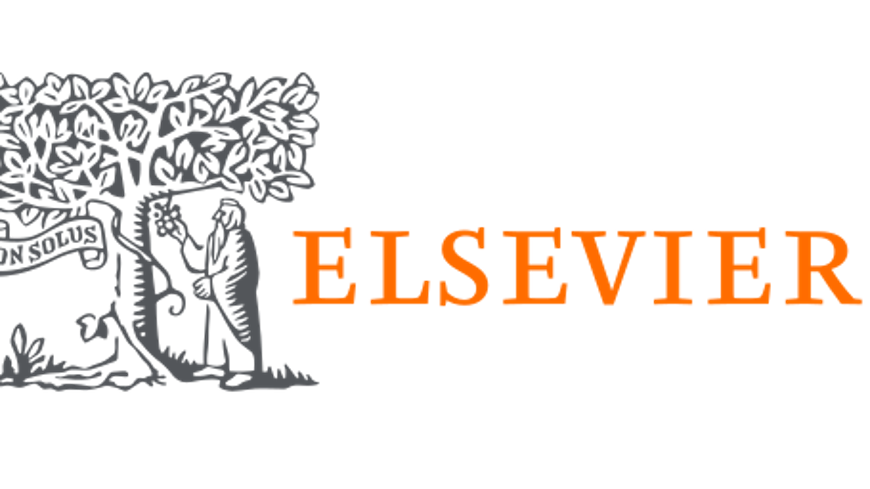
Closed-loop real-time optimization for unsteady operating production
Abstract
Environmental and economic pressure leads to an increasing desire to operate processes over various operational conditions, adapting to changing conditions such as feed quality, available energy, customer demand, or product prices. This requires frequent changes in the process setpoints, involving transitions between those. We focus on the explicit utilization of varying storage levels between process elements to increase the flexibility and thus the operational space of the overall process. To do so, we propose a so-called closed-loop static real-time optimization (RTO). It extends classical static RTO by integrating the time evolution of the storage levels and the underlying storage level controls. This enables the optimum and safe operation of the production plant, taking into account storage size limitations and filling levels of the elements. We approximate the dynamic effect of the controlled storage elements on the process dynamics by a suitable mapping, which allows us to capture the transition behavior of the storage element. The mapping can be, for instance, given by inversion-based control ideas or learned, e.g., by Gaussian processes. At the same time, the approach allows minimizing the dynamic effects of the storages on the overall system. The proposed formulation requires the efficient solution of a bilevel optimization problem. Thus, we will discuss a decomposition strategy to solve the overall closed-loop static RTO problem efficiently. A process example illustrates the effectiveness of the approach. Link